How tiny EX-certified sensors help COSL save millions through condition-based monitoring
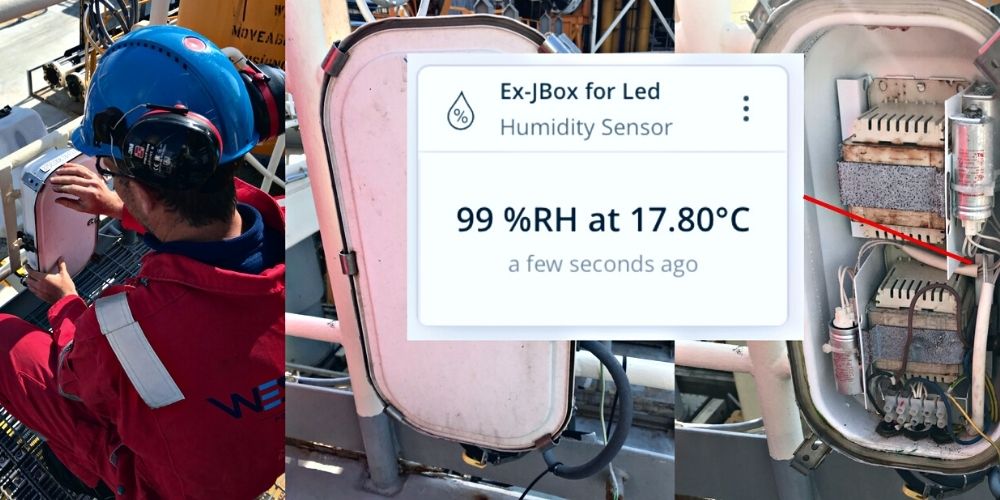
COSL, one of the most innovative production rig companies in Europe, spends a lot of resources testing new technologies. Their production rigs have technologies for automation, surveillance, digitalization, and energy-saving, and they have been working with sensor technology for many years.
COSL operates in Norway, the UK, and in the Barents Sea, and owns and operates four production rigs. Their rigs are compact, moveable, semi-submersible, and are known as the most energy-efficient production rigs on the market. They can also be operated with fewer onboard operatives than traditional rigs, making them very popular for operating companies who rent them out for various assignments.
Ex-tech Group, our sole partner for EX-zone and hazardous areas, is a Norwegian company with Global outreach specializing in delivering technologies to demanding environments. In April 2022, Ex-tech Group and COSL installed 400 sensors to remotely monitor temperature and humidity in the production rigs.
Although the project is in its initial stages, COSL is already seeing an improvement in its processes and more efficient maintenance, which they predict will save them millions.
It is a revolutionary technology, as the footprint of the sensor is so small, and the battery life is long, and this makes it very attractive to us.
Torfinn Kalstø, ICT & OT Manager at COSL Drilling Europe
Maintenance In An Extreme Environment
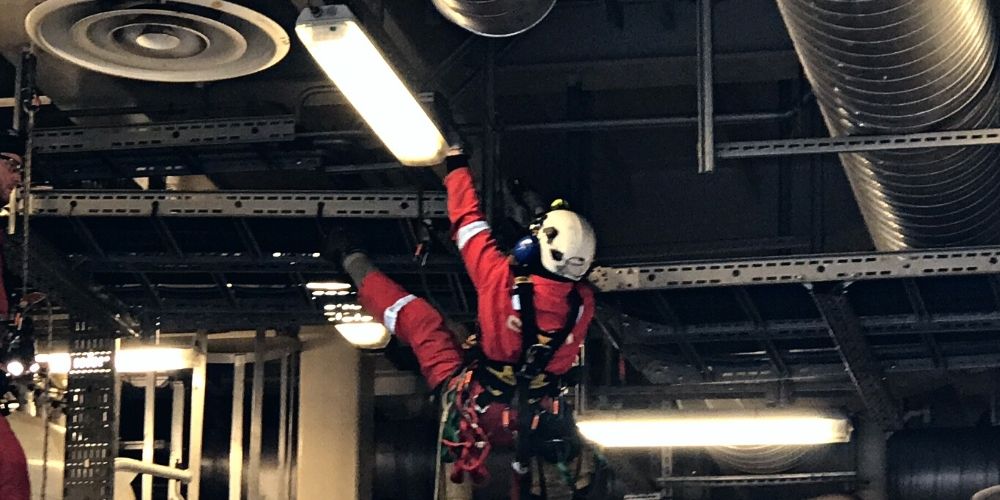
A production rig is an extreme environment where wind and weather, combined with heavy machinery, are demanding for both people and equipment. Any technology that is installed must be both robust and durable.
On any rig, there are thousands of electrical and non-electrical components, all of which must be suitable for use in explosive atmospheres. All these components need regular inspection and maintenance to ensure their integrity is preserved. Any significant reduction in performance due to faults can cause downtime and stop production, an extremely costly problem for the operator.
Inspections are required to check for critical conditions, for example, excessive humidity, that may shorten the lifespan of the unit or result in other damage. When the production rig is offshore and in operation, this is both dangerous and highly resource-intensive.
Highly trained electricians, with appropriate certifications for climbing in production rigs, must be transported, by helicopter, to the rig. They have to check every fuse box, junction box, and floodlight, some of which may be 30 meters above the platform deck. This requires additional people on the rig and is both extremely costly and time-consuming.
Rig owners are therefore striving to undertake both daily operations and periodic inspections, remotely. Some periodic inspections can also be done closer to land when the rig is between assignments.
How to Remotely Monitor Humidity
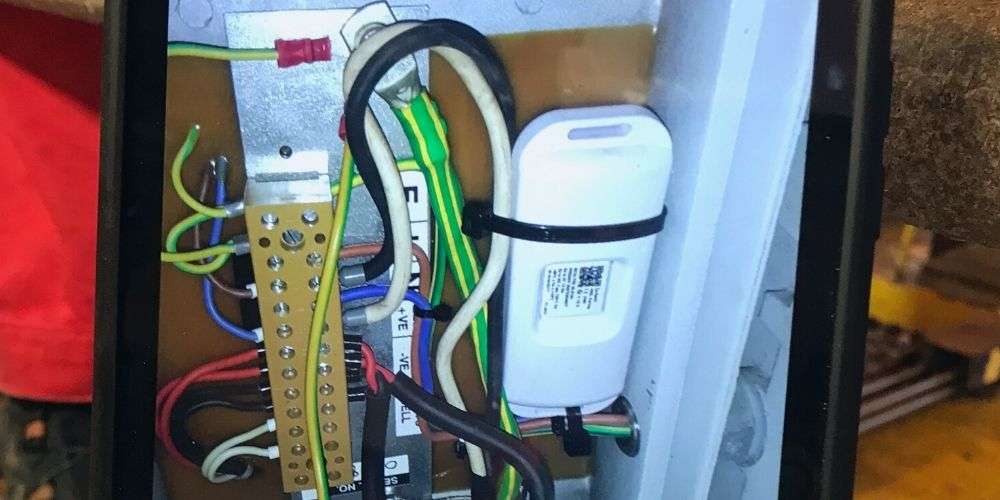
Our partner Ex-tech helps with the monitoring and reporting of humidity and temperature levels inside the electrical components, like junction boxes and floodlights. The solution is based on using small specially developed and Ex-certified wireless sensors from Disruptive Technologies, sensors that are easy and quick to install and can be retrofitted during a planned inspection.
To ensure safety compliance, Ex-tech obtained EX certification for the DT sensors, ensuring that they could be used in an environment with an explosion risk.
In April 2022, the COSL Innovator was equipped with 400 sensors whilst undergoing regular maintenance near Bergen, Norway. For this first phase of the project, sensors were installed in the junction boxes and floodlights that were physically the hardest to reach.
The data from these sensors is collected and transmitted every 15 minutes to gateways, DT Cloud Connectors, that pass it to the cloud through an Ethernet connection. The Inspectio system, which COSL uses for all inspections and operations, integrates the sensor data in its reports and sends notifications to the operators.
COSL Already Sees Benefits
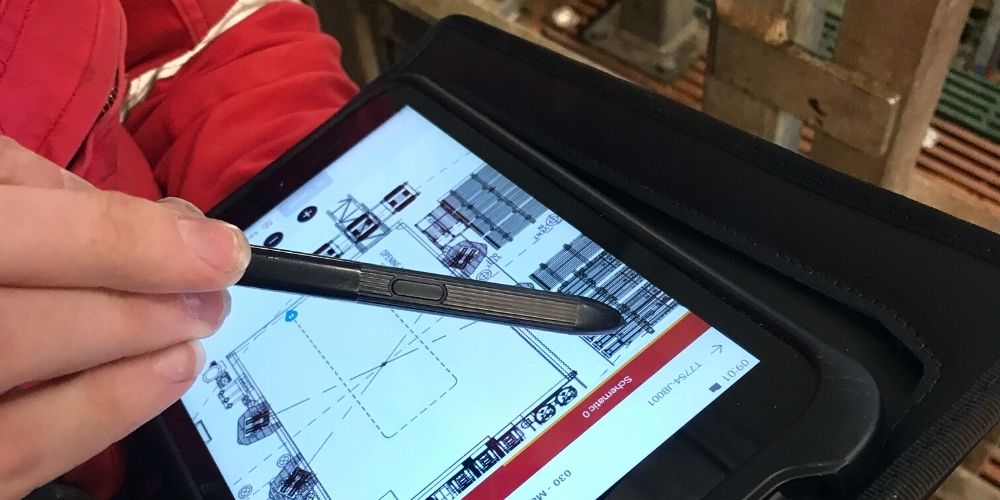
COSL has high expectations for its Return On Investment (ROI) from this project, as they can already see the resources the sensor-based system is replacing. For this phase alone, they expect to save thousands of hours on maintenance using the sensors, equating to millions of dollars in savings.
In addition, the use of the sensors reduces the risk of downtime in production and the need for people on board.
COSL expects to install many more sensors during the next scheduled inspection, after a period of testing sensor data. The COSL Innovator is now in the North Sea, undertaking a job close to England.
The benefits are split into two main areas.
Productivity, Efficient Operations, and Cost Savings
- Minimizing the risk of downtime whilst maximizing production
- Reducing the number of people on board, saving costs, and reducing risk
- Reducing the number of manual inspections and maintenance
Sustainability
- Reducing the use of helicopters for transporting certified personnel for inspections
- Prolonging the lifespan of the equipment
Capturing and retaining critical data from hazardous areas is a paradigm shift for the industry. Our proven expertise leverages data from Disruptive Technologies sensors to access complex, costly, and risky areas and provide exact status from all relevant ignition sources. Our clients can now enjoy safer and more efficient operations, a true revolution in the hazardous area space.
Jan Holm, CEO at Ex-tech Group
What’s Next for COSL & Ex-tech?
An important objective of this project is to make the sensor data available for other systems and applications, both on the rig and onshore. The information will be included in general management reports.
The data will also be integrated into the digital twin COSL has made for the production rig, visualizing the physical placement of each sensor-equipped component.
COSL is looking to expand the project to several thousand sensors on this production rig, to cover several other specific requirements. If successful the solution will be extended to their other production rigs.
COSL sees a lot of use cases for the sensors, both on the production rigs and in the industry in general. They have started with floodlights and junction boxes, as this is an easy project in which to test the sensors and, if successful, the potential cost savings will be high.

Important Features and Benefits For This Project
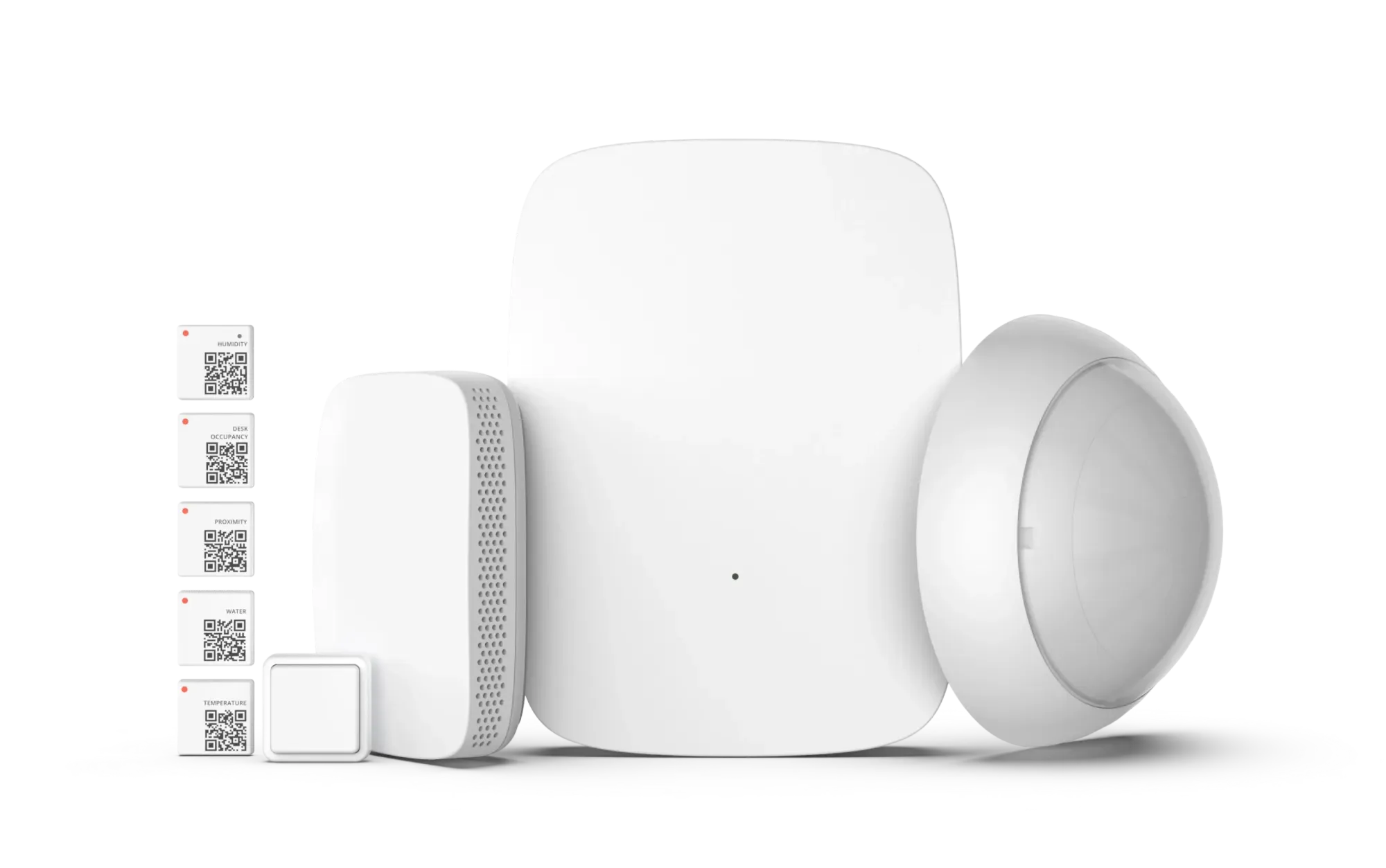
Easy-to-Deploy IoT Sensors & Infrastructure
Content That Might Interest You
Get Started
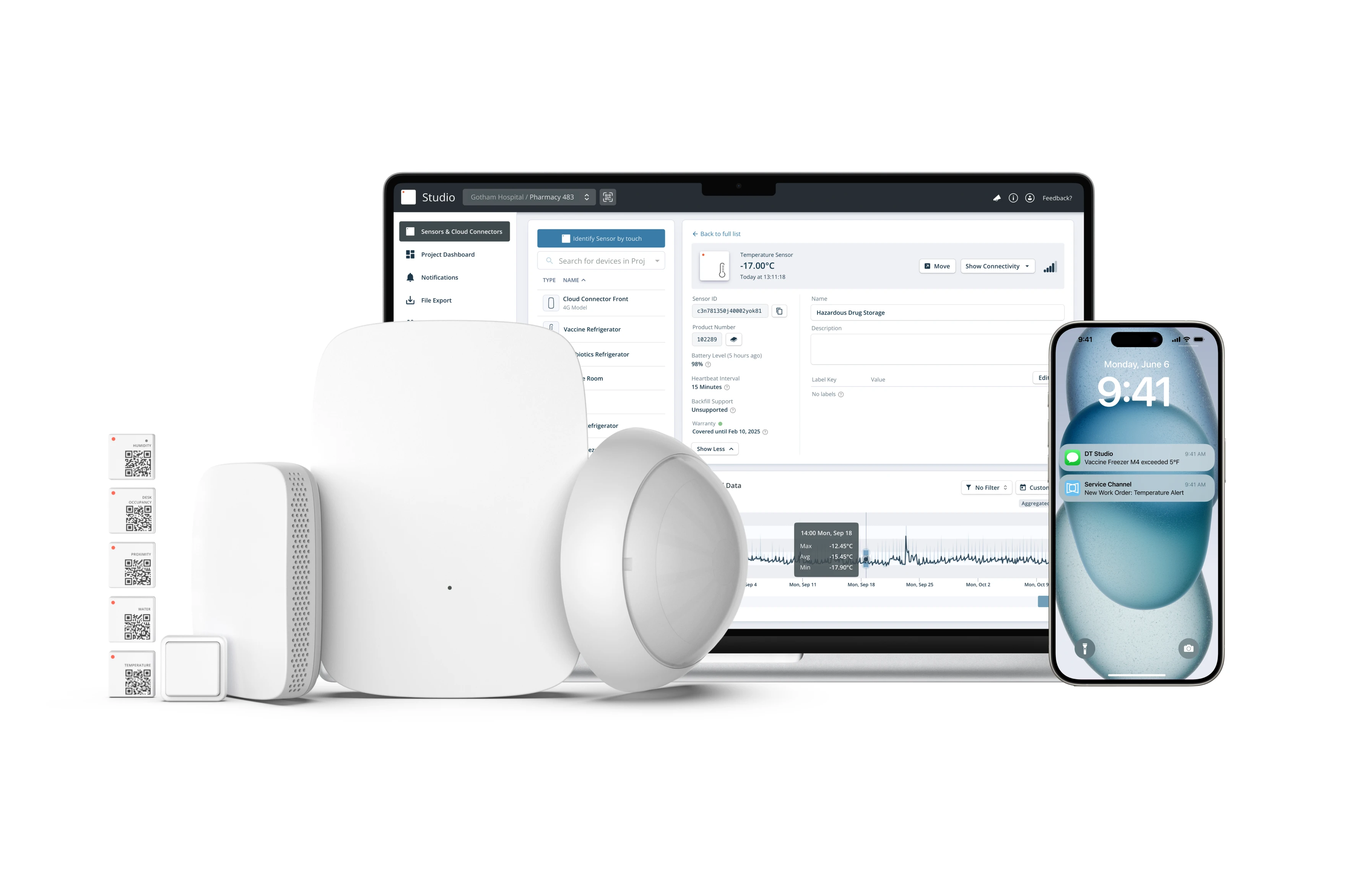